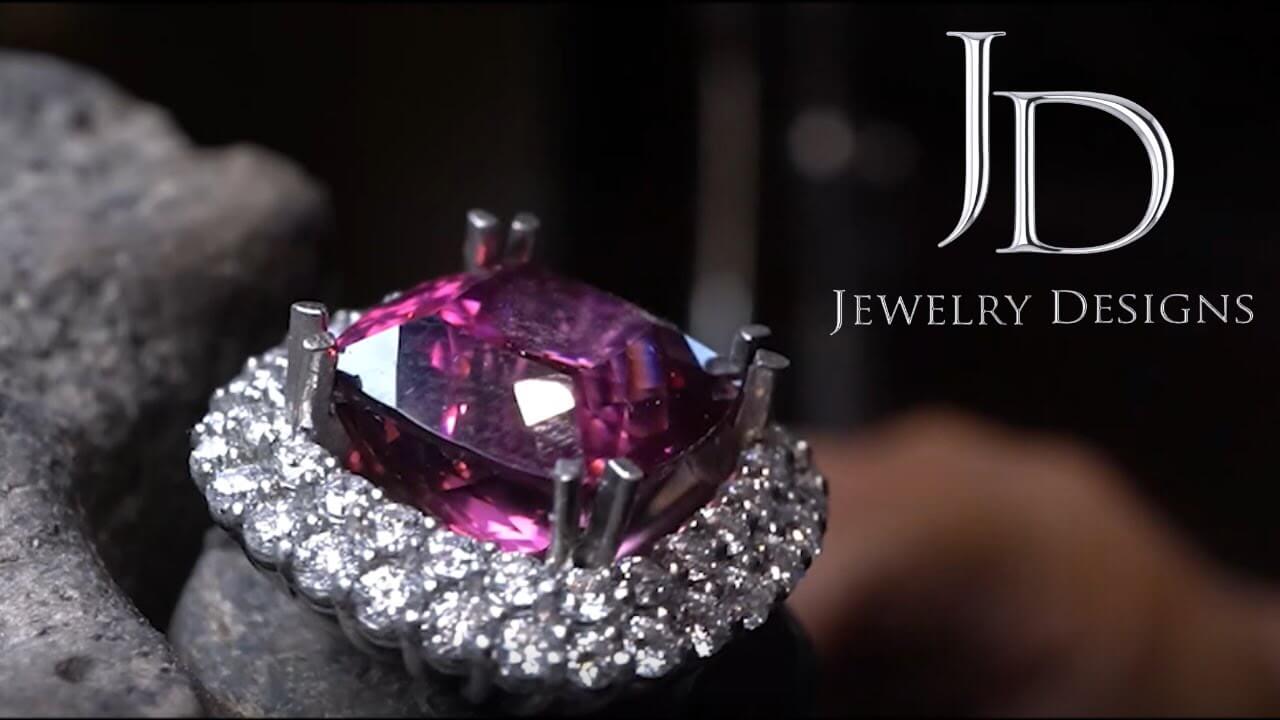
Making the Rubellite Ring
In this video, you will see artisans at Jewelry Designs making a Rubellite ring. To a jewelry designer, there are few things more inspiring than a rare gemstone. This red Rubellite Tourmaline provided all the excitement needed to create a masterpiece.
The brilliance, fire, and symmetry of the featured gem suggested that the design be simple. Therefore, we chose to frame the treasure as if it were a fine painting. With this in mind, we decided to prepare this ring with rows of brilliant diamonds. The distinct contrast of glistening white diamonds against the glowing red tourmaline proved to be alluring.
Since this is not your everyday garden variety-colored gem, the artisans chose platinum as the metal to support the stones. The neutral white color, and its durability, make platinum the clear choice.
Designing the Ring
Designing the ring required our artisans to create a computerized rendition of our vision. From this CAD rendering, they calculated the proper balance of diamonds to encircle the jewel. The goal was to stylize a minimalist design that would accentuate its beauty and portray its value. A simple, sturdy shank would wrap the finger. A wire cage gallery would support the twin rows of diamonds articulated in a soft cushion Halo.
After completing a desirable rendering, a resin model was grown on a 3-D printer. The resulting sculpture is an exact likeness of the artisan’s design. The model is grown from the specialized resin used for jewelry making. The chemical properties of this resin enable it to incinerate through the ancient lost wax casting process. A process aptly named after sculptures replaced by 3-D printing over the past two decades.
Casting the Ring
A jeweler specializing in casting will now place the hot flask in a centrifuge. The centrifuge will throw molten platinum into the hollow cavity at 3200 degrees. After the centrifuge spins to a stop, we separate the model from the investment. The rustic platinum casting that emerges from the flask is far from pretty. At first glance, it would not appear to be jewelry at all.
The resin model is suspended in a metal flask encased with plaster investment. When the investment cures and hardens, the flask will go into a furnace and cycle for many hours at temperatures ranging from 200, peaking at 1450. degrees. The extreme heat incinerates the model. Hence the name “Lost Wax Casting.” The result is a plaster-filled flask with a hollow impression of the “soon to be” Rubellite Ring.
Polish the Rubellite Ring
Now it is time to polish the Rubellite Ring. First, specialists at precious metals finishing will de-bur, grind, shape, and polish the platinum casting to bring out its beauty and luster. Next, these artists masterfully resurface the metal using files, rotary tools, and polishing wheels in many grits. Each step brings the design to life. Once the polished ring meets the level of perfection desired, it is ready for the setting of the gems.
Setting the Rubellite
Setting the Rubellite and accompanying diamonds is meticulous work requiring years of experience, vision, and steady hands. Master setters seat each gemstone into prongs at the perfect depth to provide durability while allowing each stone to project its beauty. The goal is to showcase the gems with maximum support. With so many tiny prongs, it is imperative to secure the platinum, so the stones have minimal coverage, yet optimal strength at each point of contact. It is also essential that the prongs do not snag or catch as the ring is worn.
With all diamonds level and even and the ring secure and tight, the last stone to be set is the feature gem. The setter must fit and shape talon prongs to embrace the cushion-cut tourmaline. Once aligned and secured, the ring will be polished and cleaned before final inspection.
Magnificent Rubellite Ring
The artisans now know that the glistening red jewel they started with rests in a Magnificent Rubellite Ring created by their hands—timelessly preserved to be worn and admired for generations.