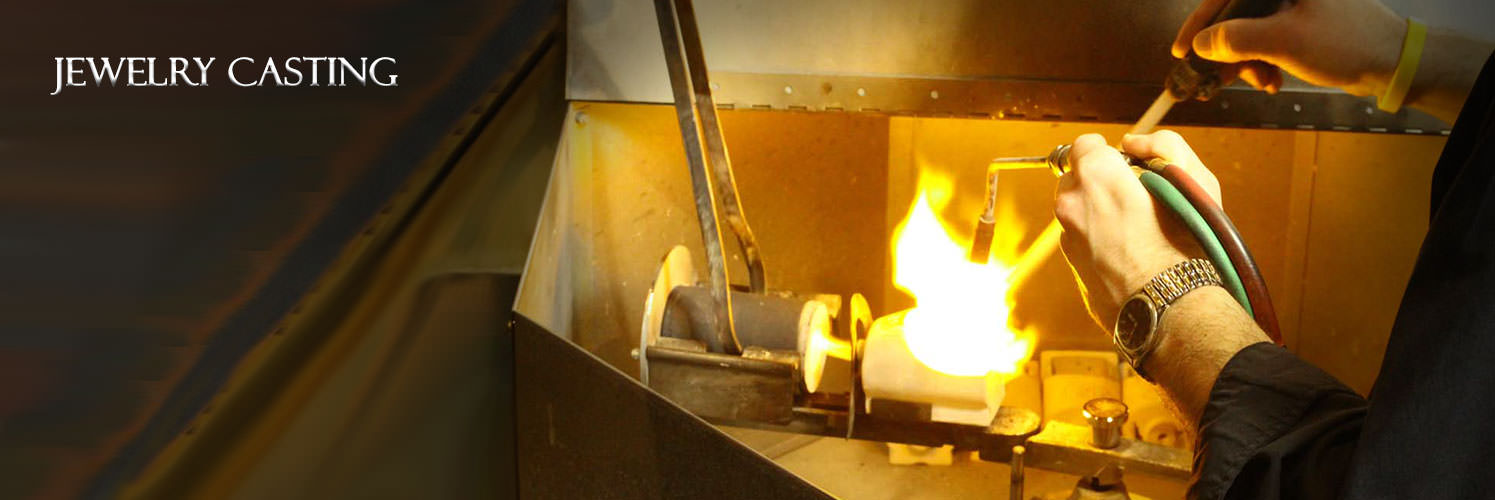
Jewelry Casting
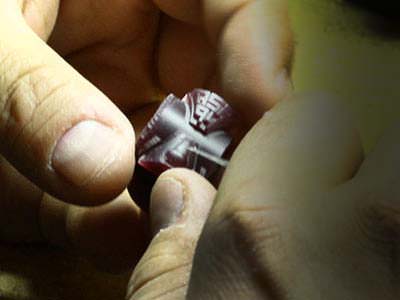
Jewelry casting is an art form that has been in existence for thousands of years. Since the time that man attained the ability to melt metal, artisans have been pouring molten gold into cavities shaped in stone, plaster, sand, and cuttlefish bone. The solidified castings were then pried, or broken free from the encasements in which they were poured by primitive craftsman who then tooled them into items of adornment.
With the advent of high frequency melting and a host of other technologies, jewelry casting is more dynamic than ever. Most jewelry casting is done through the lost wax process, whereby models created through wax carving, growing, or printing are encased in a plaster- like medium known as investment. The investment is heated to extreme temperatures to incinerate the material, creating an impression of the desired form. The intricate cavity is then filled by molten precious metal.
Gold casting and platinum casting procedures differ greatly. Platinum melts at such extreme temperatures that specialized skills, equipment and plaster investments are needed. Since gold casting encompasses a wide range of karats and colors, the alloy combinations dictate that each has temperature cycles and processes that are unique to the metal.
Burn Out Cycle
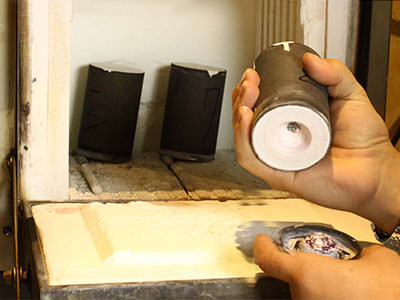
Wax models or resin type materials are connected to one another on a sprue to form a tree-like configuration. The alignment of the models is arranged to allow gold or platinum to flow through the “tree” with minimum turbulence or resistance. The “tree” is then suspended inside a metal flask and filled with plaster slurry. Once filled, air bubbles and pockets are removed from the slurry by “debubblizing” the flask inside a bell jar with negative atmosphere.
After hardening and curing, flasks containing invested models are placed in specialized ovens, where the wax is incinerated at temperatures as high as 1600° F for 12-16 hours. A properly burned out flask will have no remaining residue of wax or resin, leaving behind a hollow impression left by the tree and sculptures that were burned from it.
Centrifugal Jewelry Casting
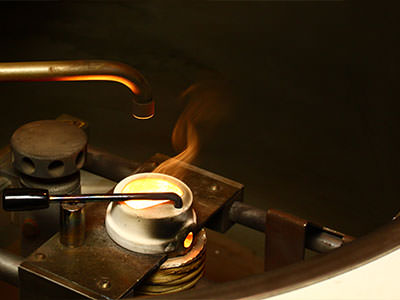
Centrifugal jewelry casting uses the force of a centrifuge to create the inertia necessary to throw gold into the hollow cavity left behind. After burn out, the flask is placed in a cradle on a swing arm in direct alignment with a crucible in which gold or platinum will be melted. Depending on the equipment and user preference, the crucible will be heated by high frequency, induction, or a torch to melt the metal, while the arm is in a cocked position. When the precious metal is at critical temperature, the centrifuge is released and metal is slung from the crucible at high velocity, filling the flask before it spins to rest.
Vacuum Casting Jewelry
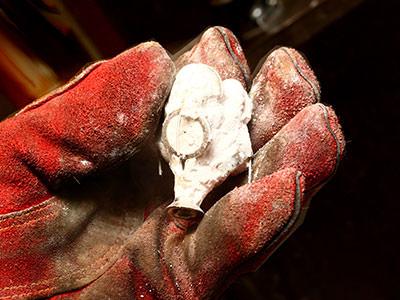
The principal behind vacuum casting is very similar to that of centrifugal casting. Once again, molten gold has to be sent with enough thrust into a flask to enable it to funnel through detailed cavities before cooling. The equipment used for vacuum casting requires the flask be loaded in a sleeve within a chamber to enable a forcible vacuum to inhale molten metal into the investment as it is being poured or released.
Precious Metal Castings
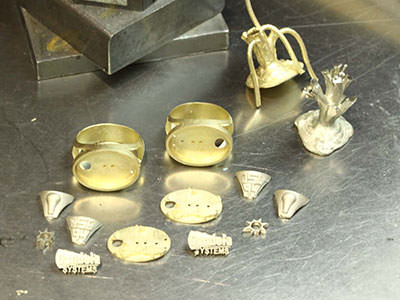
Once the flasks are filled it is necessary to remove the precious metal castings. The hollow impression in plaster, filled with glowing red platinum or gold castings, is lifted from the casting equipment with tongs. Depending on color, carat, or metal used, they are quenched in water or left to cool. When the flasks are cooled, the investment form is destroyed while the remaining plaster is chipped away, leaving behind a tree containing models as branches. The models are then cut free from the sprue and forwarded to jewelers who will execute jewelry polishing, jewelry fabrication, and stone setting to transform the casting into fine jewelry.